What is Should Cost Analysis Software?
Whenever we are going to calculate the zero-based costing of product, one thing we need to understand that “what is should cost analysis?” Should cost analysis means “cost breakdown analysis”, should costing tools are designed to help organizations assess and analyse the costs associated with their products, services, or projects.
It enables businesses to gain insights into their expenses, identify areas for cost reduction, and make informed decisions to optimize their financial performance. The should cost modeling tools allow buyers to understand breakdown of product cost into various parameter like Raw Material cost, process cost, freight cost, tool cost, OHP (Over-Head Profit) cost and other parameter based on this insight, the professionals gain an understanding of supplier’s should cost estimation along with other parameter for fair pricing and can build a transparent and better relationships with suppliers based on mutually beneficial outcomes.
The traditional should cost analysis was very manual, timely and labour-intensive process in a large organization. The objective is to determine what the cost should be, based on a thorough understanding of the various elements involved.
Modules Covered in Our Manufacturing Cost Estimation Software
1. Ferrous Casting Cost Estimation
Ferrous casting is a metal working process in which molten metal is molded into a prescribed shape, which is called die-casting. Ferrous castings are used in various industries, and play an important role in determining its cost.
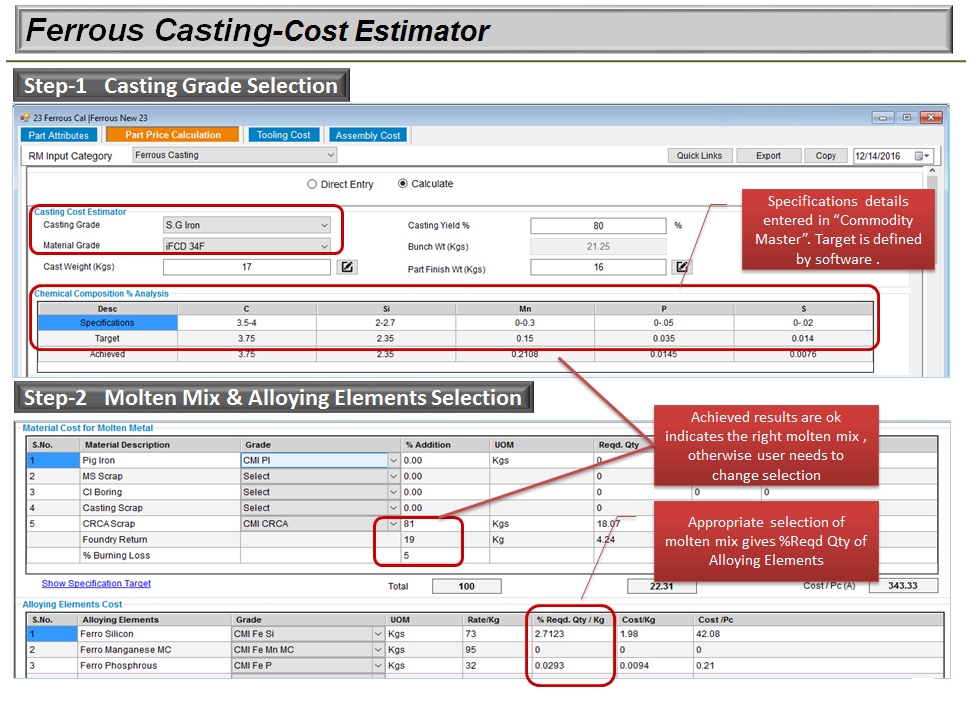
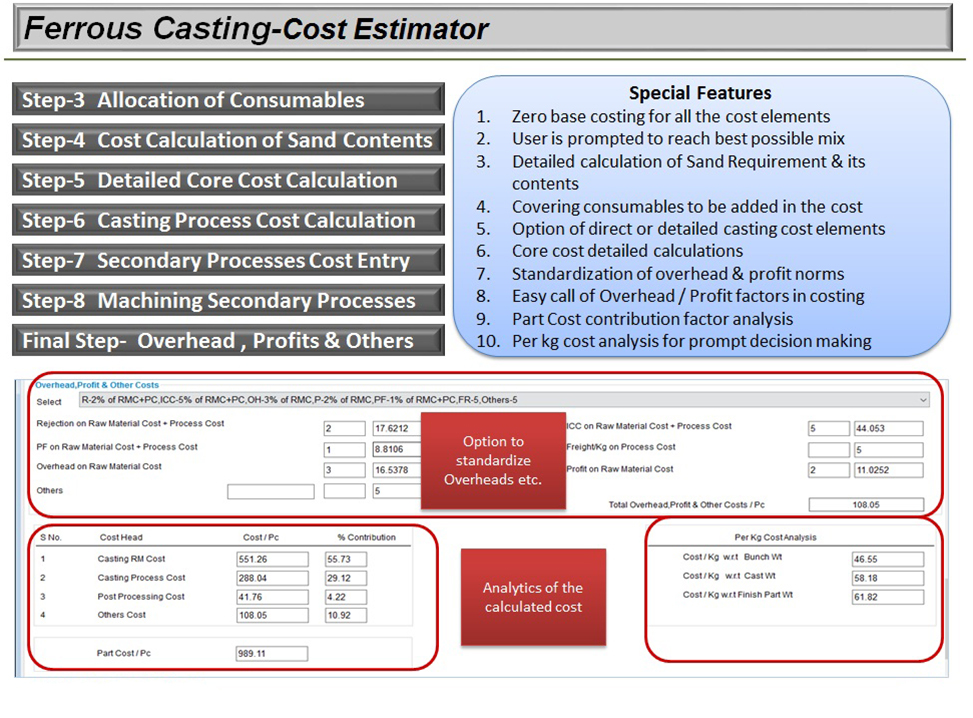
2. BOM Creation & Management
BOM is critical to manufacturing operations. A clearly drawn BOM captures the full range of components, assemblies and sub-assemblies required to manufacture a finished product. CostMasters’ comprehensive cost estimating software is optimized with robust feature-rich BOM creation and management processes.
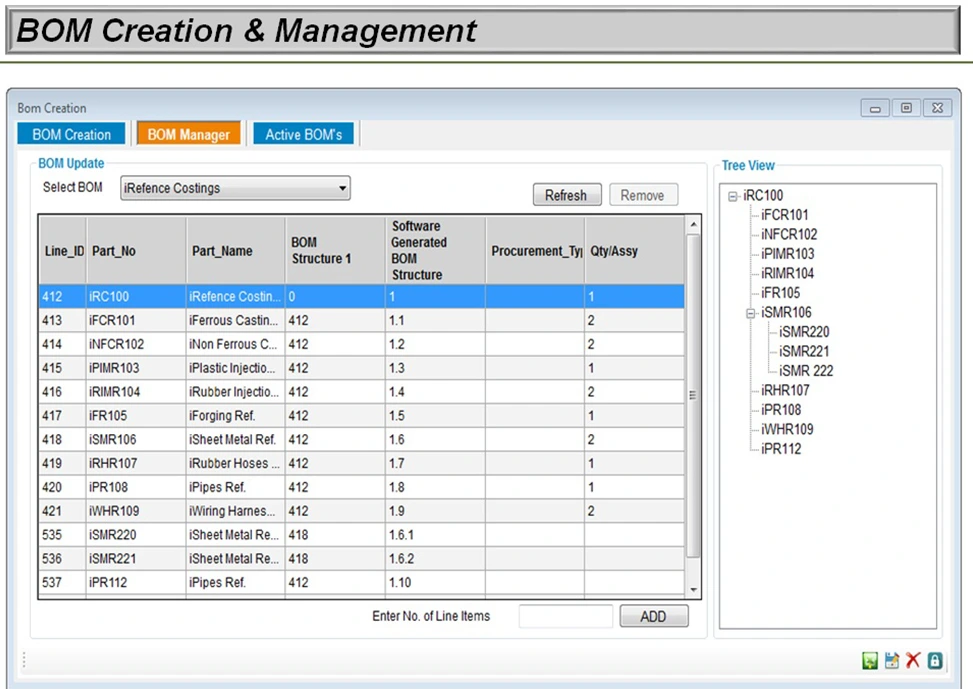
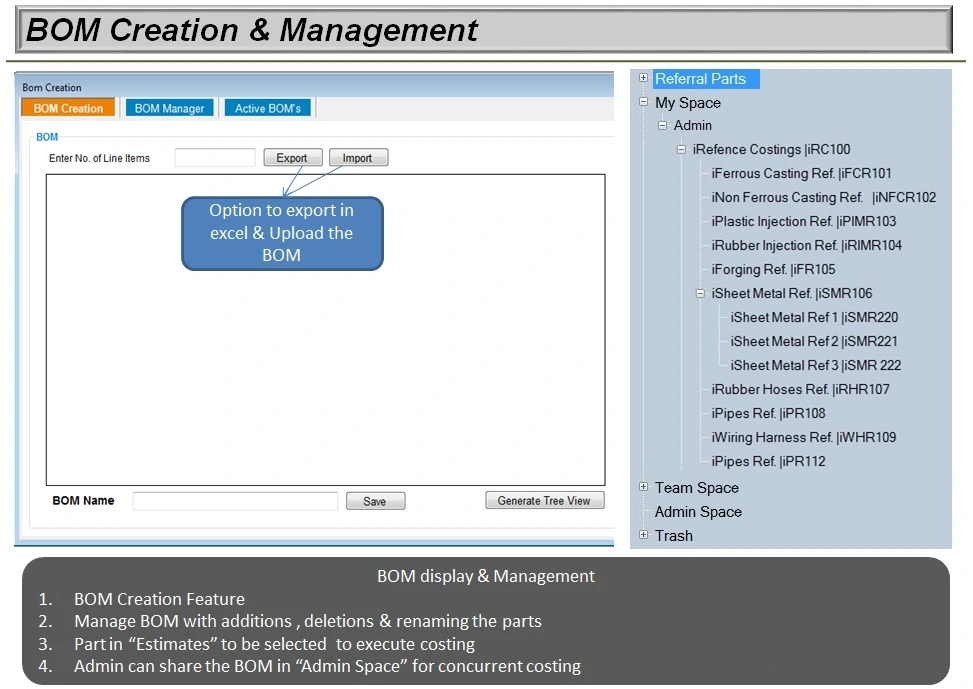
3. Plastic Injection Moulding
Plastic injection molding is a manufacturing process in which molten plastic is injected into a closed mold, Which when cooled forms a product of a specific shape. This process is widely used to make various plastic products, such as automobile parts, electronic devices, household items, and toys.
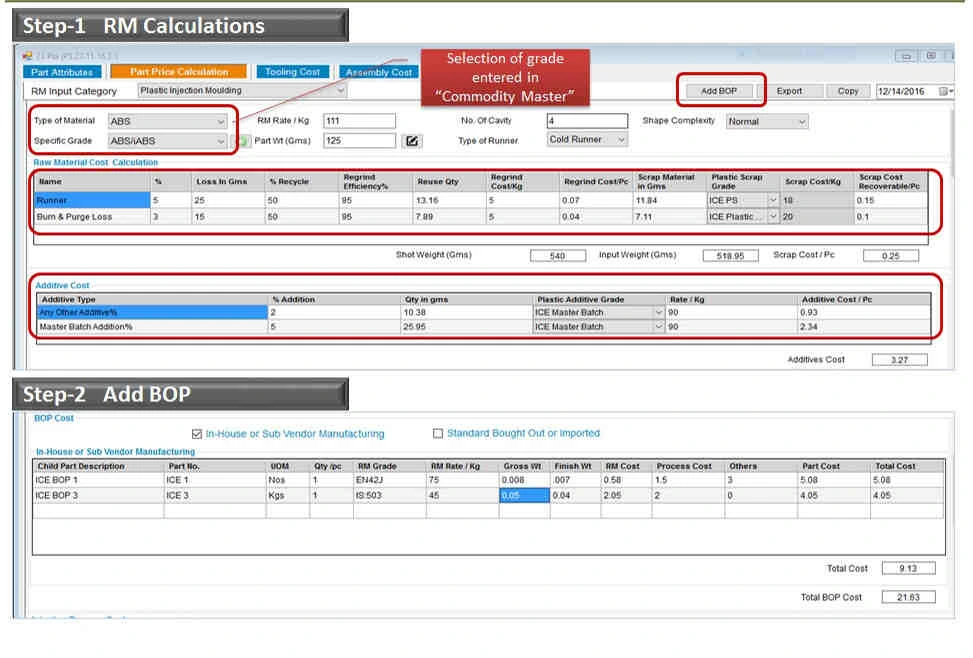
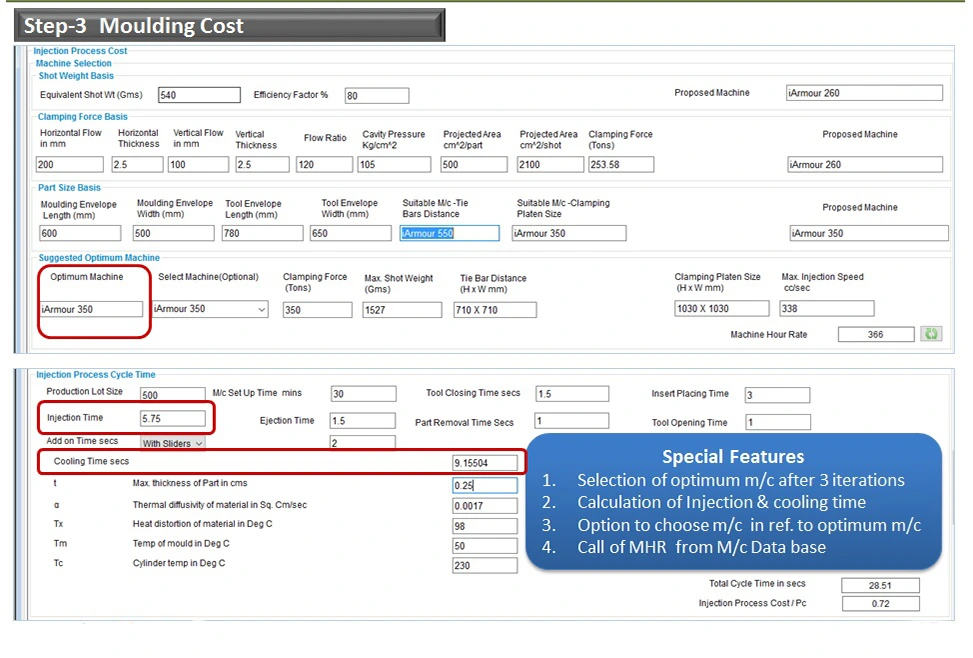
4. Machine Hour Rate Cost Calculation
CostMasters’ Machine Hour Rate Calculation software helps you calculate the hourly rate of your machines. This software takes into account essential information about your machines such as machine cost, usage lifetime, maintenance costs and other factors.
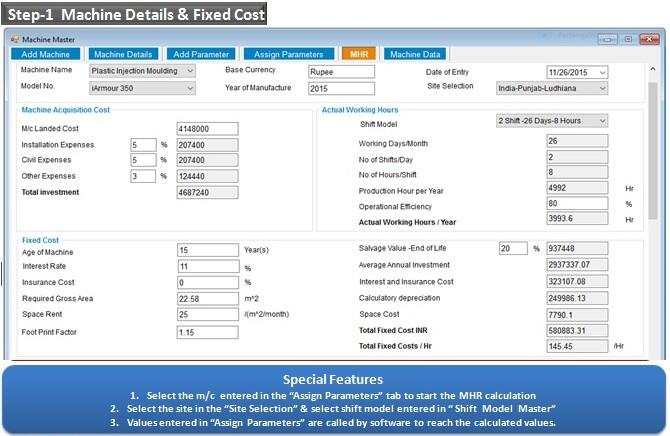
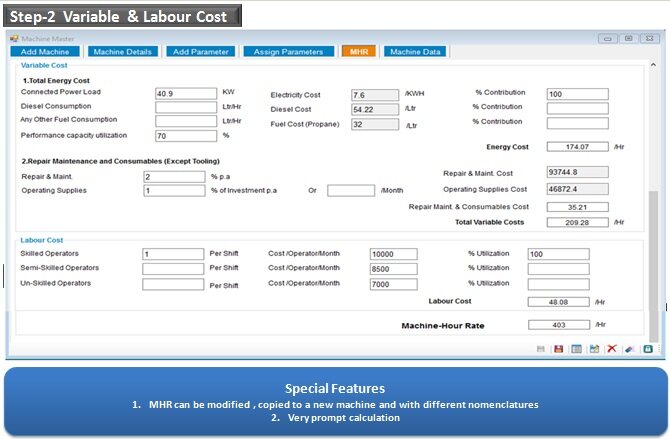
Step-by-step Guide Shown Below on How to do Should Cost Analysis:
- Define the Scope: A deep study is needed to find out what parts are required to produce the final product. Recognize every important parameter adding to the total cost of product
- Gather Data & Breakdown: Gather data from various sources about different parameter used to manufacture the product. Break down the total cost into individual component costs. Categorize costs as direct or indirect, variable or fixed such as raw material cost, cost of labour, overhead cost, tooling cost, setup cost and process cost.
- Perform Cost Modelling
A. Microsoft excel: Excel is a flexible versatile tool that can be modified for various cost analysis models. It permits users to make point-by-point cost breakdowns, perform calculations, and visualize information charts and graphs. But with these benefits there are some drawbacks also like Limited Data Handling Capacity,Limited Scalability, Lack of Centralized Data Storage, Limited Automation,Inadequate Audit Trail, Not Ideal for Raw Material indexation.
B. Should Cost Analysis Software: This kind of software design for estimation and analysing costs. These tools used database to storage of costing information, costing history, changes in various factors of costing. Based on these data the system will generate various report which can further used for optimisation the manufacturing cost estimation and provide competitive advantages to organisation.
4. Create various reports: Generate a cost overview encompassing a detailed analysis of processes, materials, additional inputs, and processing time. Incorporate estimates for non-recurring engineering costs and outline the associated amortisation expenses.
Benefits of Should Cost Analysis
Cost Reduction: should cost analysis software can identify areas where costs can be reduced. To breaking the cost in different parameter, organisation can pinpoint inefficiencies, waste, and areas for optimisation.
Negotiation Power: Should costing software empower the procurement team to have parameter-based discussion suppliers, driving better pricing agreements and contract terms. With these analysis organisations can better equipped to negotiate with suppliers with a detailed understanding of the actual cost of a product or service.
Supplier Relationship Improvement: Should cost analysis software can help to establish strong relationship with suppliers. Both parties can work collaboratively to find cost driver and areas of improvements, it will create long-term partnerships that benefit both parties.
Risk Mitigation: Should cost analysis can help to identify the risk associated with product and service chain. organisation can develop strategies to mitigate risks by understanding the cost structure and dependencies.
Value Analysis: Instead of just cutting costs, it is important for companies to also look at what suppliers offer. This wider view helps them make better choices about where they get their supplies from and who they work with.
Competitive Advantage: By utilised should cost analysis a organisation can gain a competitive advantages by optimising the cost structures and delivering products at lower prices than competitors.